The use of plastic fasteners is quite popular in manufacturing and woodworking industries. While metal fasteners have long been the go-to choice, plastic options are now proving to be just as effective in some cases.
Plastic fasteners are lightweight, corrosion-resistant, and cost-effective. They offer flexibility and can work well in specific applications. However, they may not be as durable as metal fasteners and could struggle with heavy-duty or high-stress applications.
Read on to get details about the pros and cons of plastic fasteners and how they compare against their metal counterparts.
Why are plastic fasteners used in specific applications?
Plastic fasteners are often the go-to choice for certain applications because they offer unique properties that metal fasteners can’t match. They are lightweight, quite flexible, resistant to corrosion and some chemical substances.
All these features have made them an automatic choice for various industries. For example, you can use them in marine or underwater operations where metal fixtures won’t last long. They are also the right choice for electrical systems where you need to prevent accidental power flow. Their lightweight nature helps with improving fuel efficiency and performance of automotive and aerospace systems.
We’ll discuss the use of plastic fasteners and their properties in detail in the next sections of this article.
What are the advantages of plastic fasteners?
The pros of plastic fasteners have made them a suitable option for many industries. Here’s a look at why they stand out:
Rust Resistance
Plastic fasteners don’t rust or corrode. This makes them perfect for use in harsh environments, especially where exposure to moisture or salty air is common. For this reason, they are ideal for projects that require long-term durability in challenging conditions, such as marine or coastal areas.
Safe to Use
Since plastic fasteners are non-conductive, they pose no risk of fire or explosions. This makes them an ideal choice for projects that involve electrical components, where safety is a top priority. Using them can create a safer working environment.
Lightweight and Versatile
Lightweight but strong materials are invaluable in automobile and aerospace industries. Plastics are light and since most of the fasteners are made of nylon and polypropylene, they are durable too. So, they are perfect for these heavy-duty applications.
They are also highly adaptable to different applications. Unlike metal fasteners, which can be bulky or heavy, plastic fasteners can be customized to fit just about any need. This versatility is one reason why they’re preferred in so many fields.
Available in Many Colors
Plastic fasteners can be made in a wide array of colors. This is especially helpful in projects where aesthetics matter. For example, if you have exposed screws or bolts, using plastic fasteners means they will blend right in with the color of your product.
Easy to Install
Plastic fasteners are typically designed for quick and easy installation. Their lightweight nature and snap-fit design often mean that you can install them without needing extra tools or parts. This can save time during assembly, which lowers the labor costs.
Budget-Friendly
Plastic is inexpensive to mold and produce than metal, which helps lower overall manufacturing costs. If your project requires a large number of fasteners, choosing plastic can result in significant savings. For this reason, you will see the use of plastic fastener in automotive manufacturing, where plastic screws and bolts are commonly used to keep costs down without sacrificing quality or strength.
How do plastic fasteners compare to metal ones?
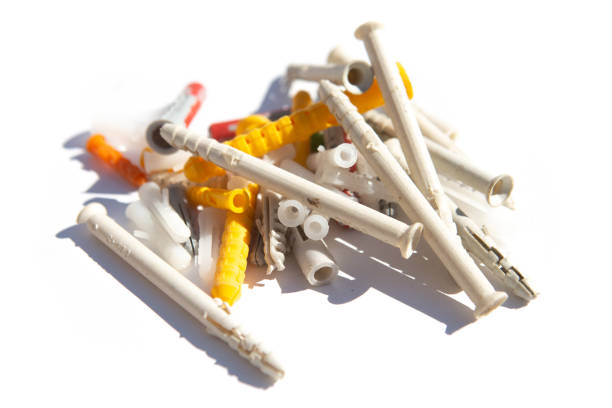
While metal has traditionally been the most popular material for fasteners, plastic-made ones are also gaining ground. Let’s compare these fasteners to assess their performance in certain situations:
Resistance to Corrosion
A plastic fastener shows remarkable resistance to corrosion. But its metal counterpart, especially in moist or salty environments, is prone to rusting and degrading over time.
Plastic materials don’t rust, making them an ideal choice for marine environments or applications where exposure to water or chemicals is a concern. For instance, plastics like PVC and PET can withstand harsh conditions like saltwater, oil, and even diesel fuel without losing their strength.
UV Resistance
Some plastics, such as polyimides and FEP, are specifically designed to handle UV radiation, making them an excellent choice for outdoor or space applications. In contrast, metal fasteners are more susceptible to damage from UV rays, which can lead to deterioration over time.
Electrical Conductivity
Plastic doesn’t conduct heat or electricity, which makes it ideal for electrical or electronic applications. This property also makes these fasteners safer to use in environments where electrical contact is a concern. They reduce the risk of short circuits or electrical hazards.
However, the electrical conductive nature of metal fasteners is useful for enabling smooth electrical current flow across connections. This is especially important in applications where grounding or maintaining electrical continuity is necessary. For instance, you can use them in a system for dissipating static electricity.
Strength and Durability
Plastic fasteners are great in certain environments, they may not be suitable for high-stress, heavy-duty applications. Plastic can deform or break under high pressure or load, which is where metal fasteners tend to excel.
Also, plastic fasteners may not have the same strength or durability in extreme conditions as metal ones, making them less reliable for certain heavy-duty or high-temperature applications.
Cost
Generally, plastic is less expensive than metal, especially when you factor in the cost of mass production. They can often be molded directly into complex shapes and even come in a variety of colors without additional processing.
In contrast, metal fasteners require several steps in manufacturing, such as cutting, stamping, and coating, which can drive up production costs.
What are the limitations of plastic fasteners?
There are also some cons of plastic fasteners, which make them less suitable for certain applications. Some of the limitations are:
Deformation. Plastic deforms under heat or pressure. It’s a soft material, so it can lose its shape when subjected to external forces, struggling to hold things together. At high temperatures, the fasteners can soften or even melt, which limits their use in places like engines or areas with extreme heat.
Shrinkage. As plastic cools, it often contracts, which can result in a fastener that’s slightly smaller than expected. Designers have to be careful about this property to ensure the correct fitting accuracy and performance of the fasteners.
Low Strength. The use of plastic fasteners is not recommended in high-stress situations. While they work well for lighter applications, they may not provide the strength needed for heavy-duty jobs. Under high load or pressure, they can break or deform, compromising the stability of the entire structure.
Low Chemical Resistance. Though some plastics do have decent resistance to certain chemicals, they can still degrade or weaken when exposed to strong acids, bases, or harsh substances.
Environmental Impact. The variety of plastic types makes recycling challenging. Some plastics are hard to break down and reuse, leading to more waste. The complexity of recycling different plastics also increases costs.
Conclusion
You can see the use of plastic fasteners in many applications because they are lightweight, versatile, resistant to UV and corrosion, and inexpensive. However, they have limitations, such as lower strength under heavy stress and potential deformation in high heat. Deciding whether to use plastic or metal fasteners depends on the demands of your project. Consider both their benefits and drawbacks to make the right choice. Need custom machined parts for your project? Zintilon provides various machining services for top-quality sheet metal fabrication, die casting, metal laser cutting, and CNC machining parts. Are you looking for a manufacturer for custom parts? Get a free quote from us!
Read Also: